Mountain sand is the sand excavated on the surface of sedimentary landforms, which has characteristics of high mud content, iron oxide content, and organic content, and is generally not used in high-grade concrete. Mountain sand divides into coarse sand, medium sand, and fine sand. Large rocks extracted from mountain sand require many processes to become mountain sand, and there are many types of raw materials. Design a reasonable production plan based on equipment cost, production scale, operation, and site. With the increasing demand for building materials, mining and processing equipment for mountain sand is also becoming increasingly popular.
Mountain Sand-Crushing Machine
Due to different processing standards, the configuration models of sand processing equipment also vary. For coarse mountain sand, it will need jaw crushers, impact crushers/cone crushers, double roller crusher, sand-making machines, and some auxiliary equipment for mountain sand processing.
1. Jaw Crusher
A jaw crusher is a commonly used primary crushing equipment in stone production lines. A jaw crusher can crush many kinds of materials, whether hard basalt or low-hardness limestone, which can be effectively processed. Jaw crusher also has wide application in mining construction industries.
Performance characteristics
- This equipment has a deep “V” crushing chamber, with fewer blind spots for stone crushing, achieving large production capacity and output.
- The crusher has a large crushing ratio and uniform product particle size;
- The gasket-type discharge port adjustment device has a wide adjustment range, is convenient and reliable, and has good equipment flexibility, which can meet the requirements of different users;
- The lubrication system is safe and reliable, with convenient component replacement and a low maintenance workload;
- The equipment has good energy-saving performance, with a single unit energy saving of 15% to 30%, double the system’s energy saving, and lower operating costs.
2. Cone Crusher
The cone crusher is a high-efficiency crusher designed based on the performance of metal materials. It has a high technological content in the stone-crushing industry. Currently, it plays a significant role in the second and third stages of crushing in mining and construction sand and stone processing, especially for single cylinder cone crushers with an hourly output of 800 tons or more, strong crushing capacity, large production capacity, which makes it very popular in sand factories.
Performance characteristics
- Multiple cavity types, covering various process requirements, SC single-cylinder cone crusher has multiple cavity types. We can select the suitable one according to your actual production needs. The cone crusher has good adaptability, to adapting to various input and output particle size requirements.
- Intelligent control system, easy to operate, fully automatic control system, continuously monitor the actual load inside the crusher, thereby optimizing the utilization rate of the crusher, enabling the crusher to achieve ideal performance at any time. In addition, the integrated design of hydraulic stations and lubrication stations also makes production operations more convenient.
- Laminated crushing, with better particle shape. Traditional crushers produce finished materials with needle and sheet shapes up to 15%. Single-cylinder cone crushing uses laminated crushing, which can reduce the needle and sheet materials content to less than 8%, resulting in better particle shape and higher strength of the discharged material.
3. Roller Crusher
The roller crusher is widely used in coal, metallurgy, mining, chemical engineering, and the building materials industry, and is more suitable for crushing raw coal (including gangue) in large coal preparation plants.
Characteristic:
- The roller crusher has reliable crushing performance. The roller crusher’s motor and reducer connect by a torque-limiting hydraulic coupling to prevent power overload. The sensor overload protection is reliable.
- It uses hydraulics for adjusting the space of the toothed roller, and centralized lubrication of the toothed roller bearings. It has the advantage of tooth shape optimization design, selection of tensile and shear forces for crushing, low consumption, and uniform grain production.
- The roller crusher has the advantages of small volume, high crushing ratio, low noise, simple structure, convenient maintenance, high efficiency, the uniform particle size of crushed materials, low over-crushing rate, convenient daily maintenance, sensitive overload protection, and high reliability.
Mountain Sand Washing Machine
1. Wheel Sand Washing Machine
The electric motor drives the impeller to rotate slowly after being decelerated by a V-belt, reducer, and gear. Sand and gravel enter through the feed chute and rolling and grinding below the impeller to remove impurities that cover the surface of the gravels and destroy the water vapor that covers the sand. At the same time, add water to form a strong water flow, remove impurities from time to time and foreign objects with small specific gravity, and discharge them from the overflow tank. Use a blade to remove clean sand and gravel, and finally pour the gravels from the rotating impeller into the discharge chute to achieve the cleaning effect of the gravels.
- Features:
① Less loss of fine sand
The wheel sand washing machine has less loss of fine sand during the cleaning process, and the grayscale and fineness modulus of the cleaned sand meet the standard requirements for building sand.
② Simple structure with the low failure rate
The wheel sand washing machine has a simple structure, with the transmission part isolated from water and sand, and almost no other wear parts except the screen. Effectively avoiding bearing failures caused by water and sand, its failure rate is much lower than the commonly used sand-washing equipment in the current market. Easy daily maintenance and short downtime.
2. Spiral Sand Washing Machine
It is generally inclined when installing a spiral sand washing machine. When it is working, the screw starts to rotate under the action of the electric motor. The sand and gravel enter the cleaning tank from the feed tank, flip and collide with each other under the drive of the screw, and then exit the impurities on the surface of the sand and gravel, breaking the water vapor layer that covers the sand particles to facilitate dehydration. Under the drive of the screw and the action of its gravity, the sand and gravel move from high to low, Clean sand and gravel entering the discharge chute through rotation, completing the cleaning function of the sand and gravel.
- Features:
① The structure is simple and reasonable, with high processing capacity and low loss during the sand washing process.
② The processing capacity is large, the production cost is low, and the single machine output can reach up to 180 tons/hour, basically meeting the sand washing requirement of our customers.
3. Trommel Screen Washing Machine
working principle:
The drum-type trommel screening washing machine consists of four pulleys, with an electric motor driving the reducer, a big gear, and a small gear driving the cleaning cylinder to rotate at low speed. Mud and stone powder are fed from the feeding port and enter the drum. The wear-resistant rubber lining plate with a certain angle in the cleaning cylinder will be cycled multiple times and washed with forward or reverse flushing water. The cleaned aggregate will be screened and sent to the discharge end, and then dehydrated. The wastewater containing sludge will flow through a porous baffle at the discharge or feed end.
- Features:
The Trommel screen sand washing machine requires a large amount of water and also has a large processing capacity. Reusing the cleaned sewage can achieve the effect of water conservation.
200tph Mountain Sand Wash Plant
This setup is a 200tph mountain sand wash plant. It configures with one set of vibrating feeder DN4911, one set of Trommel screen GT2055, one set of fine crushing jaw crusher pe-250*750, two sets of spiral sand washer 2XL-915, one set of xs3610, 1 set of fine sand recycling machine, 1 set of double roller machine 2pg800x600, 4 conveyors and two sand pumps.
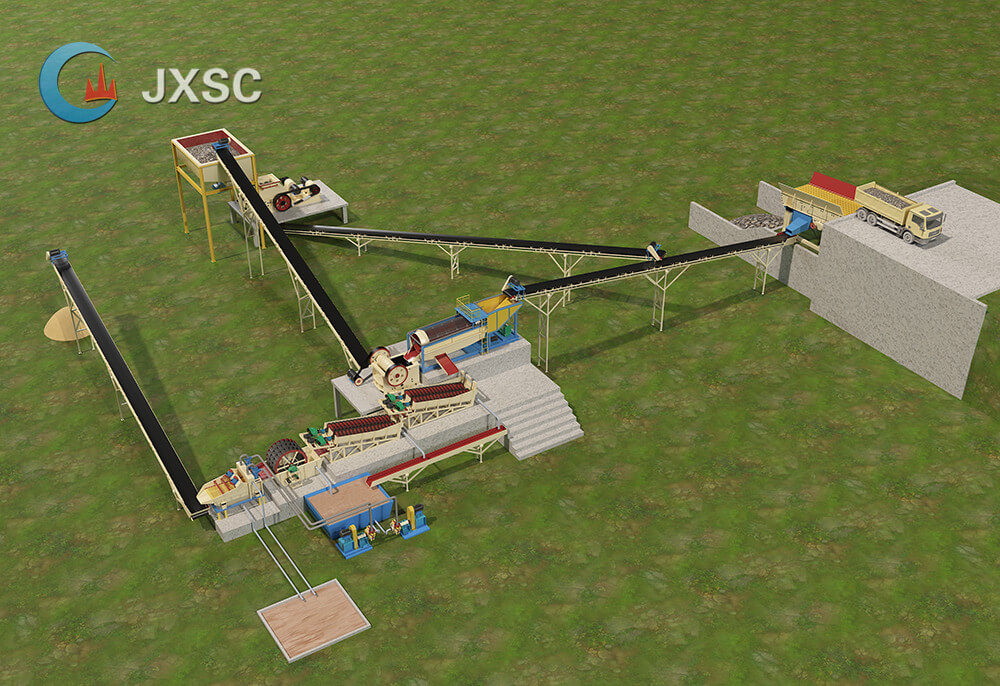
Since there is much clay in the raw material, there are four-stage sieve-washing procedures:
- The truckload the raw material goes to the vibrating feeder, and the vibrating feeder screen the stones larger than ≥210mm by the screen bar, and <210mm stone will go to the trommel screen to wash and separate.
- the 0-5mm material will go to 2 stage spiral sand washer for washing, then go to the wheel bucket and washer to wash again.
- the 5-210 mm will be sent to a fine crushing jaw crusher for crushing to 0-25mm, then to the double roller crusher for crushing to 0-2mm. The 0-2mm material will go from the first conveyor to the trommel screen.
- The sand from the wheel bucket sand washer will be sent to the fine recycling machine to dewater. Tailings of the trommel screen, sand washers, and fine sand recycling machine will be sent to the wheel sand washer to wash again and go to the recycling machine to dewater. After dewatering, we can get the high-grade sand as required.
The mountain sand processing line also needs auxiliary equipment, such as vibrating feeders, belt conveyors, slurry pumps, dewatering screens, etc. JXSC provides a complete set of sand processing equipment. We will design the process based on your different input sizes, product, and finished product requirements for sand. Welcome to inquire!